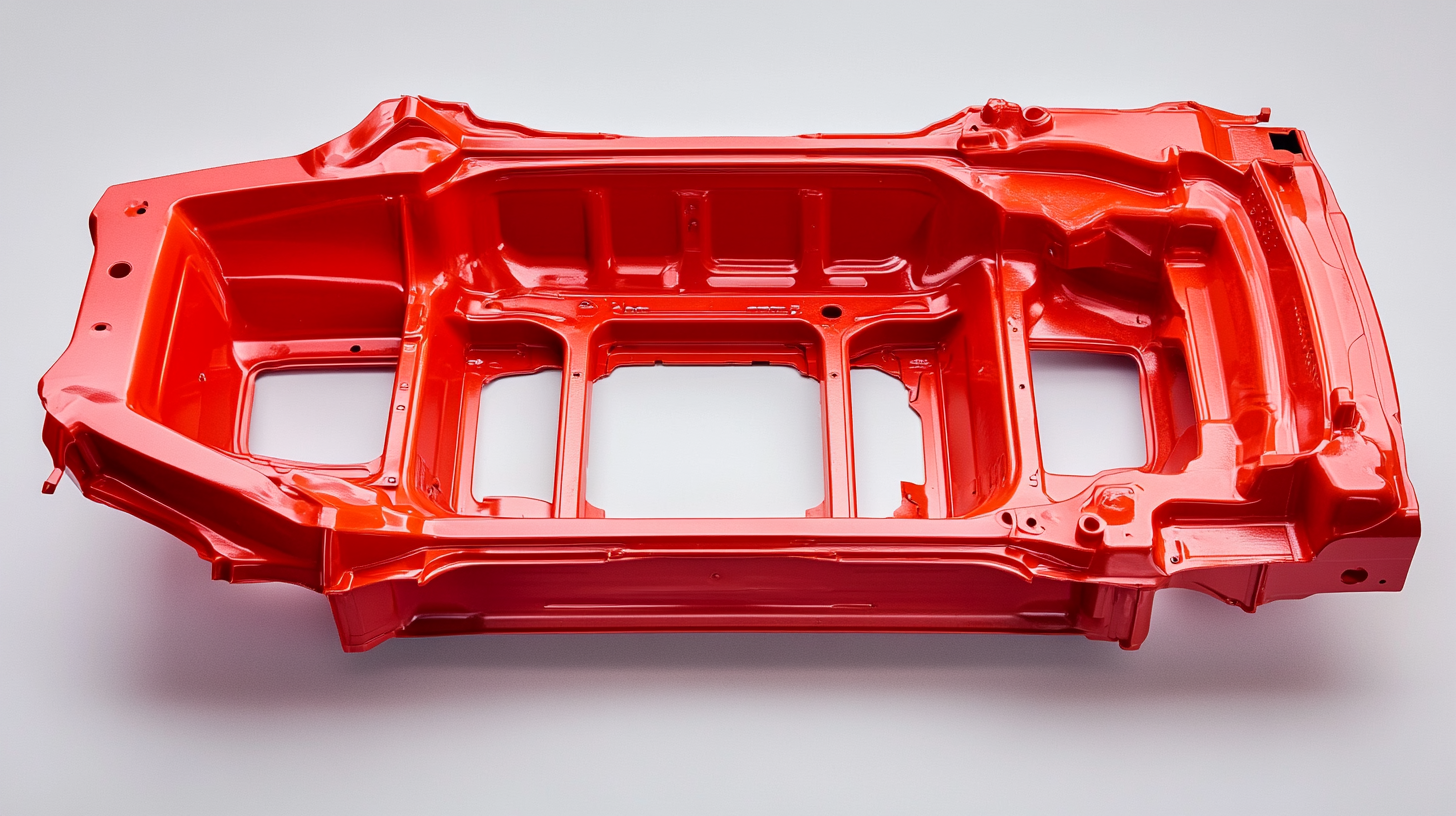
Injection molding plays a crucial role in modern automotive manufacturing, enabling the production of high-quality, durable, and lightweight components at scale. This process is essential for producing complex parts with precision, reducing manufacturing costs, and ensuring consistency in mass production. From interior trim to under-the-hood components, injection molding is the backbone of automotive part production.
Let’s explore why injection molding is indispensable in the automotive industry and how it drives efficiency, innovation, and cost-effectiveness.
How Does Injection Molding Improve Automotive Manufacturing Efficiency?

Injection molding enables the rapid, large-scale production of automotive components with minimal waste and high precision. Compared to traditional manufacturing methods, this process offers shorter cycle times, allowing automakers to produce thousands of identical parts in a fraction of the time.
Key efficiency benefits:
High-Speed Production: Multiple parts can be molded simultaneously, reducing overall production time.
Automation & Repeatability: Advanced robotic systems streamline the injection process, ensuring each part is identical.
Minimal Material Waste: Excess plastic can be recycled, making the process cost-effective and sustainable.
For automakers, efficiency is everything—reducing production times means lower costs and faster vehicle assembly.
Why Is Injection Molding Ideal for Lightweight Automotive Parts?
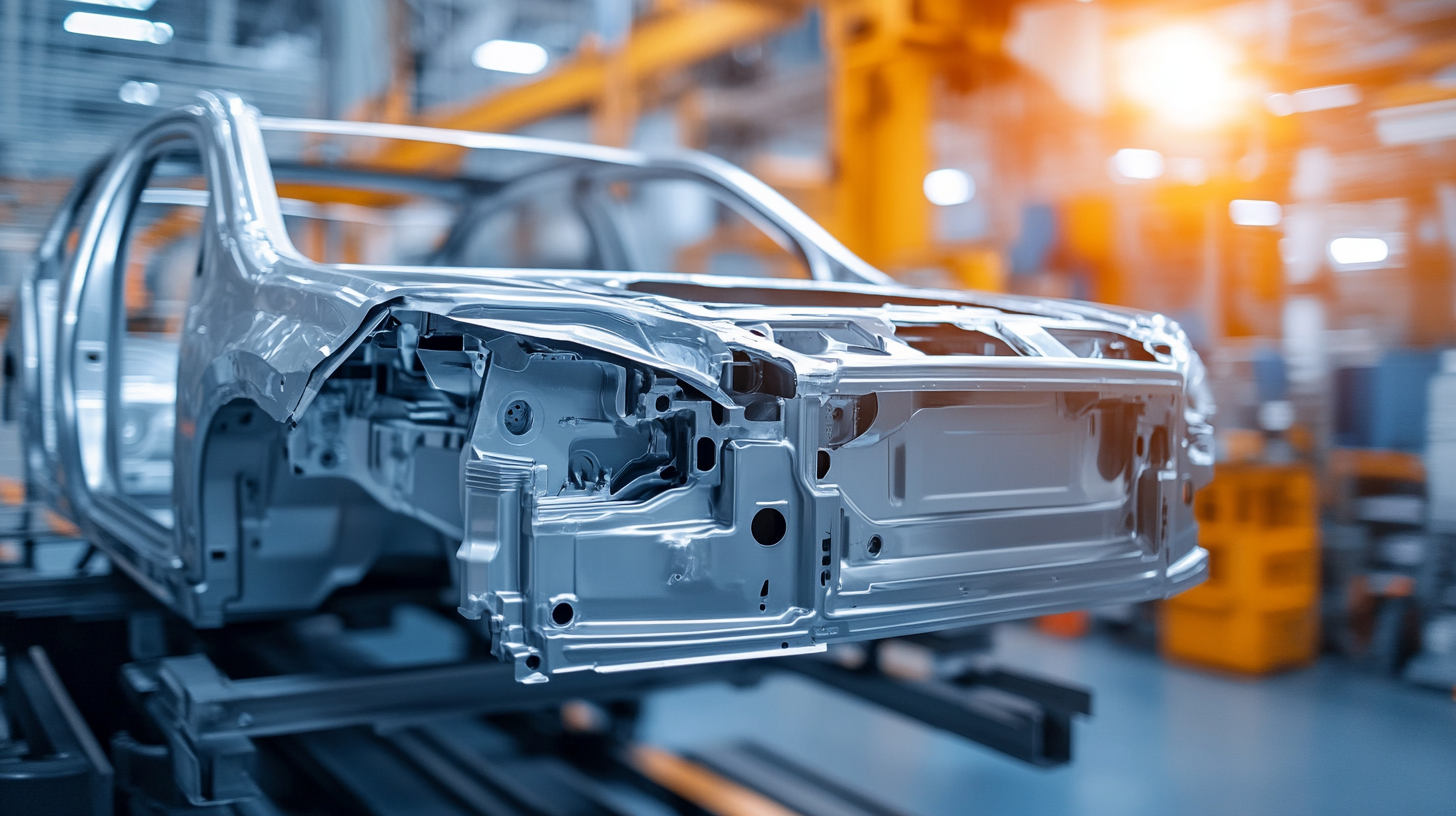
Injection molding allows manufacturers to produce lightweight plastic components that replace traditional metal parts, improving fuel efficiency and vehicle performance. With stringent environmental regulations, automakers are increasingly shifting towards lighter materials to reduce carbon emissions.
Common lightweight plastics used in automotive molding:
Polypropylene (PP): Used for bumpers, dashboards, and door panels.
Acrylonitrile Butadiene Styrene (ABS): Ideal for interior trim and structural components.
Glass-Filled Nylon: Used in under-the-hood applications due to its strength and heat resistance.
By using lightweight yet durable plastics, injection molding contributes to improved fuel efficiency and lower vehicle weight.
How Does Injection Molding Enhance Design Flexibility?
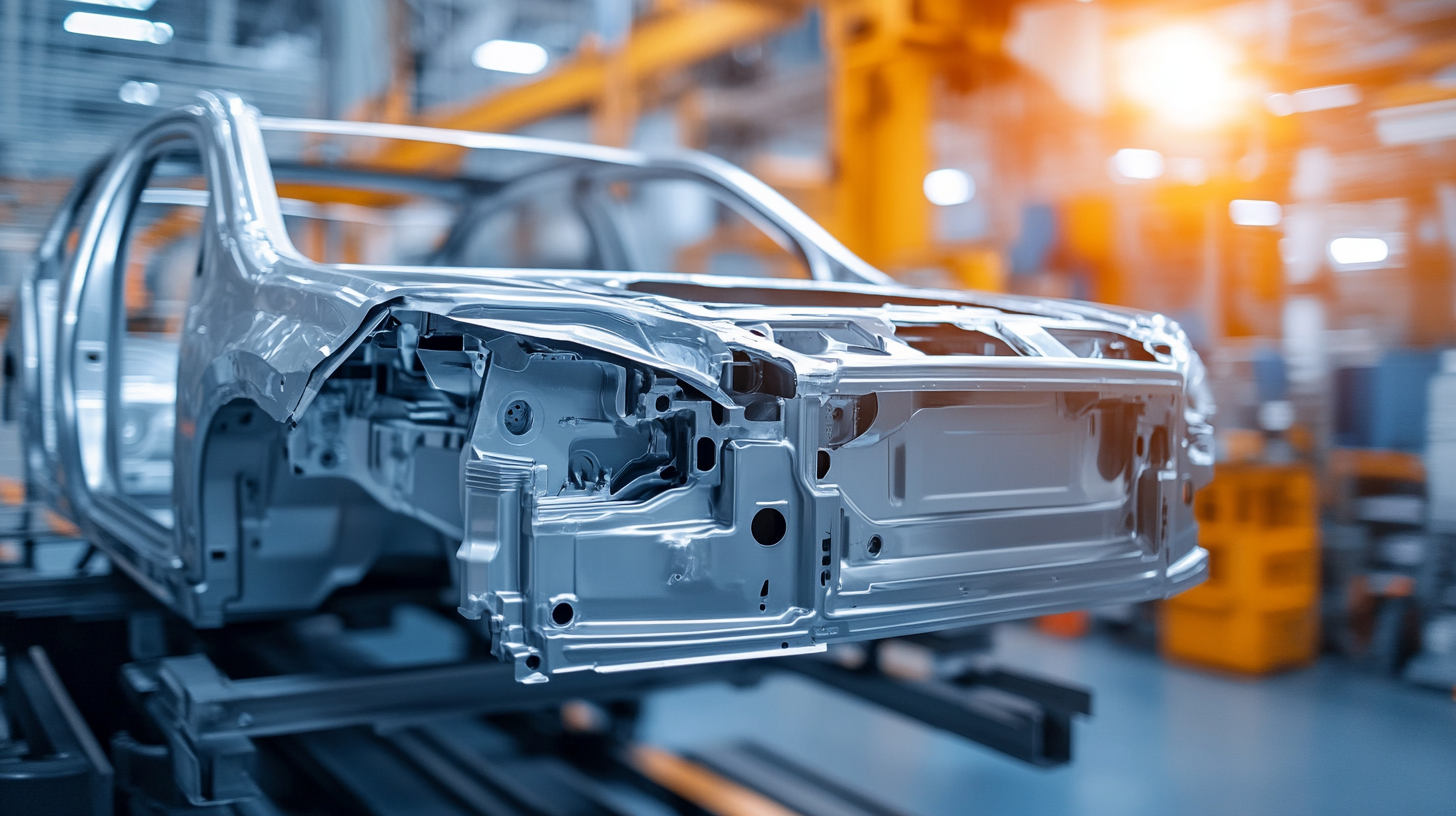
The versatility of injection molding allows automakers to create intricate and highly functional parts with precision. Unlike metal stamping or machining, injection molding offers greater design flexibility, enabling manufacturers to integrate multiple features into a single component.
Advantages of design flexibility in injection molding:
Complex Geometries: Supports intricate shapes and thin-walled designs that would be challenging with other methods.
Customization: Automakers can modify molds to create different variations of a part for specific models.
Integration of Features: Clips, hinges, and fasteners can be molded directly into the part, reducing assembly costs.
This flexibility allows automotive manufacturers to push the boundaries of design while maintaining cost efficiency.
What Automotive Components Are Commonly Made Using Injection Molding?
Component Type | Example Parts | Material Used |
Interior Components | Dashboards, door panels, center consoles | ABS, PP, Polycarbonate |
Exterior Parts | Bumpers, grilles, side mirrors | PP, Glass-Filled Nylon |
Under-the-Hood | Air intake manifolds, engine covers | Nylon, PEEK, PPS |
Electrical Components | Connectors, battery housings | Polycarbonate, ABS, Thermoplastic Elastomers |
How Does Injection Molding Reduce Production Costs?
Injection molding offers significant cost advantages over traditional manufacturing techniques by reducing labor, material waste, and cycle times. While the upfront cost of tooling can be high, the per-part cost decreases substantially in high-volume production.
Ways injection molding lowers production costs:
High Production Efficiency: Multiple identical parts can be produced in a single cycle, reducing per-unit cost.
Reduced Assembly Needs: Integrated part design eliminates the need for additional fastening or welding.
Lower Material Costs: Plastics are often cheaper than metals and require less energy to process.
For automotive manufacturers, cost savings translate to higher profitability and competitive pricing in the market.
Key Benefits of Injection Molding in the Automotive Industry
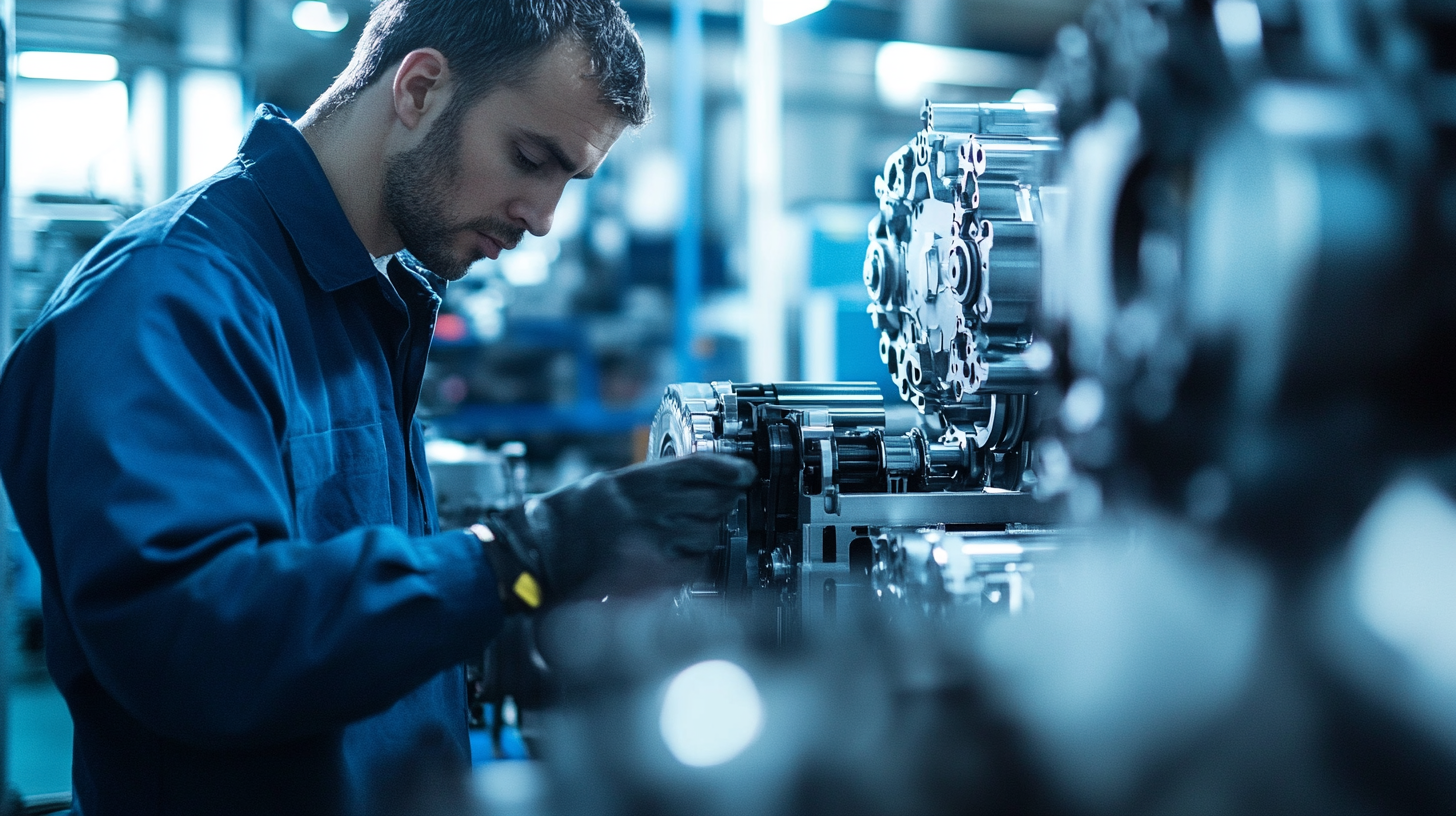
Mass Production Capability – Enables high-speed manufacturing of complex components.
Lightweight Parts – Helps reduce vehicle weight for improved fuel efficiency.
Superior Design Flexibility – Allows for innovative and intricate designs.
High Durability & Strength – Produces components that withstand extreme conditions.
Cost-Effective Production – Minimizes waste and reduces labor costs.
Conclusion
Injection molding is an indispensable manufacturing process in the automotive industry, offering efficiency, cost-effectiveness, and design flexibility. By enabling mass production of lightweight, durable, and complex components, it plays a crucial role in modern vehicle manufacturing.
For expert guidance on automotive injection molding solutions, visit our resource center or contact us. Let’s drive innovation in automotive manufacturing together!
Post time: Feb-25-2025